什么是铸造?类型、优点、缺点和应用
所属地区:信息补充中
发布日期:2025年07月01日
在多种金属零件制造工艺中,金属铸造以其复杂形状、材料多功能性和大批量生产能力而闻名。但 铸造到底是什么?铸造是将金属和合金原料熔化后倒入预先设计的模腔中,然后凝固,从而将其转化为所需功能部件的过程。同时,模腔是预期部件几何形状的镜像。
铸造技术有很多种,每种技术都有独特的特点和优势;砂型铸造、模压铸造和熔模铸造就是其中几种。但是,使用哪种方法取决于设计部件的原材料类型和规格。本文将讨论铸造工艺、技术、兼容的金属和合金、优点和缺点,以提供全面的概述。
什么是铸造?
它指的是熔融金属在凝固时形成几何形状而制成的任何金属和合金部件。液态金属会呈现出包含它的腔体的几何形状。浇注后,材料会流过腔体(模具)内的每个角落并捕捉每个细节。然后,将部件顶出到模具腔体中。
追溯其历史,铸造工艺可追溯到七千年前(约公元前3200年) 在古代 美索不达米亚和中国 将铜转化为各种有用的物品。公元前 645 年后,砂型铸造成为工具和炊具最突出的制造方法之一。
在现代制造时代,随着金属铸造工艺能力的不断发展,它已融入所有行业。它可以以低廉的价格制造精密而复杂的部件,尤其是在大批量生产中。模具、铸模或其他形式的型腔可以生产数千到数百万个相同的零件。然而,砂模和熔模只能使用一次,这对于原型项目来说是经济的。此外,铸造部件保留了原有的机械和物理性能。
铸造是如何进行的?
铸造工艺的基本工作机理
铸造或铸模工艺涉及两种不同的方法,使用腔体模型和可承受多次循环的精密模具。以下是与其工作相关的一些术语;
模型:这是用金属、塑料或木材制作的用于塑造模具的所需部件的全尺寸复制品。
型芯和型腔:型腔是指勾勒出铸件外部特征的空心部分,而型芯则形成内部特征,例如孔和通道。
浇注系统:引导和控制金属液从浇注炉流向型腔的通道。它包括浇口、流道和浇口等组件。
冒口:模具中的储存器,用于将熔融金属供给铸件以补偿凝固过程中的收缩,确保铸件无空洞和缺陷。
接下来我们来一步步阐述一下casting的工作原理。
步骤 1:创建模具型腔
图案是创建空腔所必需的,因为它充当所需形状的主体。复制品或图案可以用木头、塑料或蜡制成。随后,在图案设计和制造中需要考虑一些因素,例如尺寸调节以适应收缩余量、拔模角度以方便拆卸、空心部分的芯模等。
制作完模型后,将其放入一个造型盒中,四周环绕着沙子或陶瓷等造型材料。然后,它会捕捉形状并在弹出时离开型腔。然而,永久模具型腔是采用先进的制造技术制成的,例如 数控 和 电火花加工 不锈钢或铝。
步骤2:倒入熔融材料
首先,材料熔炼涉及电弧、感应或坩埚,具体取决于铸件尺寸。例如,大型铸件需要大型熔炉来熔化原材料,并在浇注前使用小型钢包进行转移。
浇注是通过手动操作坩埚或机械和液压倾倒来完成的。然而,连铸机可以在模具沿着生产线移动时自动将熔融材料倒入浇注底座。温度根据铸造材料的熔点而变化。例如,不锈钢铸件高达 1000℃-1250℃。接下来,浇口和浇注系统将液体材料引导到型腔。
第四步:冷却固化
一旦液态金属捕捉到所有腔体的细节,它就会在特定时间内冷却并凝固。冷却系统可能涉及通道和通道来控制冷却速度。同时,冷却时间取决于铸件的尺寸、复杂程度和材料类型。
在凝固过程中,被称为晶核的微小固体颗粒聚集在一起并开始晶体生长,最终形成相应材料的晶粒结构。这种机制允许恢复原有的性能。
步骤 4:取出铸造产品
最后,将产品从模具中取出。如果模具是可膨胀的(砂型或熔模铸造),操作员或机械系统会将其破坏以弹出最终部件。另一方面,对于可重复使用的模具和冲模,顶出机构会取出金属铸造产品。然后,清洁和后处理可确保尺寸精度和成品质量。
现在我们知道了什么是铸造以及它的基本工作机制,让我们来讨论一下铸造的类型有哪些。
不同类型的铸造方法
随着各行各业不断寻求更精确、更复杂的铸件,金属铸造技术也在同时开发新方法和新技术。您可以找到多种类型的铸造方法,例如砂型或硅型铸造和压铸方法,每种方法都具有一些独特的功能。这些技术的比较分析(流程、优势和应用)可以帮助您确定哪种技术最适合您的项目。
以下是制造业中常见的铸造方法。
砂模铸造
砂型铸造法使用紧密堆积的细小硅基材料或砂粒来制作模具。模具包括两个部分:上模和下模(上半部分和下半部分)。同时,将熔融金属倒入由这两个部分形成的型腔中。这种机制还可确保精确对准、易于操作、复杂形状和高效浇注。
产品优点
模具制造和铸造工艺简单,且工具成本非常低。
砂型铸造几乎与所有合金都兼容,包括黑色金属和有色金属。
形状和尺寸灵活。可铸造重量超过200吨的零件。
虽然尺寸精度较低,但后处理简单且耗时较少。
应用: 活塞、衬套、电子元件、阀门、轴承、发动机曲轴箱、工厂机械等。
精密铸造
- 熔模铸造工艺 比砂型铸造相对复杂。它涉及使用连接在中央蜡浇口中的蜡模来准备模具。然后,陶瓷等耐火材料围绕该网络。接下来,加热模具将耐火材料内的蜡模熔化,并使型腔具有光滑的表面,这也是它也称为失蜡铸造的原因。然后,将液体倒入该型腔中,并在凝固完成后破坏模具以取出零件。
产品优点
使用蜡模可以制作空心部分、底切和内部通道,而无需插入芯。
晶粒结构细化,表面光洁度更好。
尺寸精度高(±0.1mm)
具有复杂几何形状的薄壁零件
应用: 军用和飞机部件,如发动机零件、工业设备部件、汽车发动机和排气系统、医疗植入物和仪器等。
压铸
这种铸造使用由坚固的材料制成的永久模具(称为模具),例如硬化工具钢。它通常用于锌、铝、铜和锡等材料。 压铸工艺 包括在熔炉中熔化原材料,熔炉可能连接到铸造机,也可能不连接到铸造机。然后,液压柱塞或注射机构将液体输送到模具中。同时,压力可达到 25000 psi。
产品优点
整个生产周期内严格的公差和一致性
后期处理操作要求较低
大批量生产具有成本效益
应用: 它的应用范围很广,例如汽车零件、飞机涡轮叶片和机身、电器外壳、工业产品、机床和家用电器等。
离心铸造
离心铸造法或旋转铸造法使用绕轴旋转的圆柱形模具,将液态金属倒入旋转的模具中。离心力将浇注的金属推向模具壁,形成均匀的层。然后,凝固形成具有特定厚度的模具形状。
产品优点
由于金属液连续供给,因此不存在孔隙
由于离心铸造部件向内凝固,因此出现气穴和缩孔的风险极小。
由于没有冒口,因此减少了浇注阶段的材料消耗。
致密且均匀的谷物结构。
应用: 这种铸造制造主要用于制造对称物品,例如空心圆柱体,轴套,管道,压力容器,圆盘形状等。
低压铸造
附在铸造机上的浇注炉或加压炉的压力通常为 0.02 至 0.07 Mpa。浇注炉保持在铸件下方,用升液管将金属液压到上方,然后将其转移到型腔中。持续的压力是填充型腔所必需的。一旦型腔被填满,冷却通道就会以受控的方式冷却模具,直到完全凝固。
产品优点
低压可以精确控制填充并消除湍流,减少孔隙率和收缩等缺陷。
高精度和精细的铸造。
低压铸造工艺适用于铝合金等各种有色材料。
光滑的填充还可以铸造尖角和复杂的几何形状。
应用: 气缸轮毂和框架、轮毂、厨具、定制空心和复杂型材、配件、电子设备部件等。
重力压铸
重力压铸工艺中的金属浇注不需要压力注射或柱塞机制。它涉及利用重力将材料从熔炉或钢包转移到模具中。在填充完成之前,没有其他力影响流动。此外,它主要适用于熔点较低的有色合金,例如铜、锌、铝和镁。
产品优点
定义结构、更好的机械性能和表面光洁度。
由于没有压力流,最终部件的孔隙率最小。
由于不需要注射机制,它比其他永久模具具有更简单的工具。
应用: 重力压铸在许多行业中具有广泛的应用,包括汽车零部件、工业机械零件、航空发动机和外壳元件、装饰品、家用电器零件等。
真空压铸
顾名思义, 真空铸造工艺 将熔融状态的金属或塑料放入真空中成型。一般来说,在此过程中,泵或类似装置会抽走模具内的所有空气。
硅胶模具(如聚氨酯)用于橡胶和塑料成型。但是,其他类型的模具和压模也适用于真空铸造不同材料。此外,这种铸造制造模仿了注塑技术的一些特性。这种真空铸造策略也适用于标准压铸,以最大限度地降低空气滞留的风险。
产品优点
高精度和准确度,特别是对于 3D 打印模具的项目。
铸工精细,细节复杂
它消除了铸造金属内部形成孔隙的风险。
能够很好地铸造较薄壁的零件
应用: 功能塑料原型、医疗植入物和假肢、消费品、汽车车身面板和其他部件、食品加工部件等。
挤压压铸
该方法通过在模具内压制液态和半固态材料来制造零件。首先,液态金属填充加热的开放式模具,然后上部零件将其关闭并通过连接的液压板或其他合适的机制施加压力。零件在压力下凝固并提供更好的机械性能特征。此外,它也被称为液态金属锻造。
挤压压铸有两种类型:直接压铸和间接压铸。在直接压铸过程中,熔融金属填充模具,上半部分闭合模具。另一方面,间接压铸首先将熔融金属注入型腔,然后通过冲头或柱塞施加高压。
产品优点
优异的表面纹理和最小的孔隙率。
生产周期快。
挤压铸造可以生产出精确的(接近最终形状的)零件。
压制过程中的快速传热可产生精细的微观结构。
应用: 高强度汽车零部件(如底盘和发动机支架)、航空航天零件、工业齿轮和液压部件、医疗设备零件等。
消失模铸造
“消失模”之所以被称为“消失模”,是因为所需部件的聚苯乙烯泡沫模型负责产生最终形状。模型被放置在耐火材料内,在倒入液体材料后,耐火材料会熔化,并在凝固后形成形状。然后,打破模具就会露出部件。
产品优点
具有优异的表面质量和最少的后加工要求的复杂几何形状。
消失模铸造可与多种材料兼容,包括铁、不锈钢、铝和铜。
它简化了制造过程,减少了时间、劳动力和材料浪费。
应用: 用于测试的快速原型、汽车气缸盖和焊接件、管件、阀门、泵外壳等。
连续铸造
连续铸造包括在生产线上连续浇注、凝固和部件移除。设置和过程涉及钢包或熔炉,材料通过控制系统流入模腔。随后,模具中的冷却机制(水道)迅速降低温度。因此,在使模具部件明显冷却的同时,进一步喷水使它们恢复到室温。
产品优点
这是一个简单的过程,因为连续铸造不需要流道、浇口和冒口。
100% 额定产量,无材料浪费。
连铸自动化提高了效率和生产率。
应用:具有一致轮廓的零件,如梁、柱、棒、带、管等。
铸造所用材料
多种铁和有色合金适用于金属铸造工艺。下表简要说明了铸造材料、其特性和等级。
金属/合金 铸造等级 抗拉强度 抗疲劳 硬度 耐磨性 耐腐蚀性
镁 AZ91D、AM60、AM50 中 好 中 中 中
铝板 A356、6061、7075 中 优异 中 好 优异
铁 灰铸铁 (G3000)、球墨铸铁 (65-45-12) 高 高 高 高 低至中等
锌 锌合金 3、锌合金 5、ZA-8 中 低 中 中 好
铁板 碳钢 (AISI 1020)、不锈钢 (304、316) 优异 优异 优异 优异 中等至优秀
铜合金 黄铜(C36000)、青铜(C95400) 高 好 中 高 优异
铅合金 铅锡合金、铅锑合金 低 低 低 低 高
铸造的优点
复杂的形状和几何形状
铸造工艺可以创建复杂的形状和特征。例如,内部通道和腔体、底切、薄壁、空心部分、多部件组件、不对称几何形状等。同时,这种能力背后的原因是熔融金属可以在任何小腔体和尖角内流动。
材料的多功能性
它可以与多种金属和合金一起使用, 黑色金属和有色金属。例如,铁、钢、锌、铜、铝和铅合金。因此,广泛的材料多功能性使人们能够灵活地选择满足所需特性的最佳材料。此外,铸造难以加工或锻造的金属也很容易实现。
成本效益
对于小批量或原型,砂型铸造和其他膨胀型铸造具有成本效益。另一方面,永久压模铸造方法适用于大规模制造,因为一次性模具成本可以覆盖数百万个周期。总体而言,铸造是一种经济高效的制造方法。
尺寸范围
任何尺寸的部件都可以铸造,从几百克到 200 多吨。例如,小型摩托车发动机缸体到大型蒸汽涡轮机外壳和工业设备底座。
高强度和耐用性
通过控制冷却过程使模具凝固,确保晶粒结构均匀,并在所有方向上保持相同的机械性能(强度和韧性)。此外,热处理和合金化等先进技术可提高耐磨性、耐腐蚀性和整体耐用性。
减少浪费
浇口、进料口和流道产生的废料可通过重新熔化在后续循环或批次中重新使用。因此,铸造制造中的材料浪费最少,从而降低了生产成本并有利于环境可持续性。
铸造的缺点
初始成本和时间
模具安装成本和时间比其他制造方法的加工成本更高,尤其是永久性模具。它会影响小规模生产的单件生产成本。较长的安装和生产周期也会影响从设计到上市的时间。
表面光洁度和精度
在砂型、耐火材料铸造的工艺中,由于造型材料的特性,铸件表面常常粗糙,尺寸不一致,因此铸件产品需要进行修整、打磨等后加工。
缺陷和质量控制
在金属铸件中,可能会因滞留气体、流动湍流、冷却不均匀、质量控制过程复杂以及其他原因(例如孔隙、收缩、翘曲和夹杂物)而出现缺陷。这些缺陷会削弱物理结构和性能。
复杂过程控制
铸造的另一个缺点是工艺控制的复杂性,控制温度、流速、压力、冷却速度和固化时间等许多参数使得准确控制工艺变得具有挑战性。此外,熔融材料的冶金性能考虑也增加了复杂性。因此,缺陷品的百分比和后处理要求可能会增加。
铸造的工业应用
压铸件
接下来,让我们从多个领域的应用角度来谈谈铸造是什么。
汽车行业
从“压铸方法最初是为了制造复杂的汽车锌部件而发明的”这一事实可以看出,汽车行业铸造应用的多样性。在当前情况下,汽车严重依赖铸造技术来生产轻质耐用的部件,这些部件有助于提高燃油效率和性能,例如发动机缸体、气缸盖和传动部件。铸造能力可以使用插入芯和定制工具方法精确地制造这些部件的复杂性和复杂特征。同时,铝压铸有利于生产轻质耐用的部件。
由铝铸造而成的高强度、轻量化发动机部件。
底盘部件动力传动部件。
空调零件。
燃油进气系统、转向系统、变速箱等。
航空航天工业
铸造方法可以将镍基超级合金、铝合金和镁合金等轻质材料加工成复杂的航空航天部件。同时,受控的冷却和凝固增强了它们的性能。因此,它通过生产轻质耐用的部件使航空航天业受益,从而提高了飞机和航天器的燃油效率和性能。
因此,熔模铸造在航空航天工业中最为常见。然而,模具、消失模、砂型和其他铸造方法也很普遍。铸造工艺允许制造具有复杂几何形状和内部冷却通道的航空航天部件,例如发动机缸体、气缸盖和传动部件。其他应用包括:
发动机部件、涡轮叶片、燃油系统零件、起落架零件等。
泵壳入口和出口蜗壳。
液压系统元件。
控制室内部及部件。
消费品
铸造工艺能够制作复杂的设计,例如华丽的装饰、精致的厨房用具和耐用的炊具,因此适合制作许多消费品。这些物品采用熔模铸造、模铸、消失模铸造和砂型铸造等技术制造。由于精细的细节和美观性在这些应用中至关重要,因此铸造方法还可以确保腔壁表面光滑。
装饰品、墙钩、相框、灯具等。
门把手、门把手和其他类似的硬件。
厨房用具,例如锅铲、开瓶器、水槽水龙头、搅拌机底座和炉灶燃烧器。
工业设备和机械
铸造制造保持了原材料的原始特性,甚至可以通过添加填料和添加剂来提高其性能。因此,砂型、模具和其他铸造模具可以塑造高强度和耐腐蚀的合金,如不锈钢、碳合金和铝。此外,铸造还适用于大尺寸和重量的设计。因此,铸造可以为重型机械和工业设备生产坚固、耐用、耐磨和耐腐蚀的零件。例如,泵、变速箱、阀门、液压缸组件、破碎机颚式破碎机、传送带滚轮、定制外壳等。
医疗器械
生物相容性材料铬、钛、锆和钛合金也可以使用不同的技术进行精确铸造。精密铸造零件具有出色的光洁度、精度和复杂特性,这些特性对于医疗植入物和手术器械来说是必不可少的,以确保患者的安全。同时,砂型、模具和其他类型的模具也用于制造设备外壳、诊断设备部件和医疗家具。
其他一些具体的应用示例是;
定制髋关节置换、膝关节、脊柱和牙科植入物
心脏瓣膜框架、镊子和手术刀
手术剪和手术托盘
MRI 机器外壳和 CT 扫描仪框架
能源行业
不锈钢、镁、铝和锌合金等高强度材料的铸造可以为能源行业制造出能够承受高压力和恶劣化学和环境条件的部件和产品。此外,熔模铸造和压铸等工艺可确保精度和一致性,并将缺陷降至最低,这对于能源工厂的可靠性至关重要。
风力涡轮机部件,如轮毂、变速箱壳体和主机架,采用砂型和熔模铸造,具有高精度和结构完整性。
涡轮叶片、轮叶和燃烧室具有复杂的细节和严格的公差。
核反应堆压力容器、堆芯围带和蒸汽发生器零件。
太阳能电池板和电动汽车组件。
铸造与注塑成型的比较
铸造与注塑成型对比
从根本上讲 注塑工艺 同样是依靠熔料在预定形状的型腔内凝固的原理,但具体机制、能力、材料兼容性等各方面都有所不同,接下来分别阐述什么是铸造、什么是注塑成型,从中可以看出深度上的差异。
注塑工艺
这是一种主要用于批量生产热塑性塑料部件(少数热固性塑料和金属除外)的制造技术。液态塑料或金属在高压下注入模腔;材料在模具内流动,并在凝固后带走模腔的细节。此外,顶针或其他系统将部件从模具中取出。通常,注塑模具由高强度钢合金制成。
性能
各批次尺寸和整体质量一致
大批量时具有成本效益
生产周期快
高度自动化是可能的
它可以容纳二次插入物和其他类型的材料以形成单一物品。
缺点
对于小批量生产来说,高昂的工具和设备成本在经济上是昂贵的。
质量和结构完整性比铸造产品低。
材料的多功能性仅限于聚合物和少数金属。
大尺寸部件不适合注塑成型。
适合的应用
高强度汽车零部件、精密航空航天硬件、工业厂房机械、可靠能源组件、重型设备、医疗植入物等。
铸造过程
铸造,尤其是压铸模具与注塑成型相对相似;您可以将压铸模具与注塑模具联系起来。然而,压铸与注塑成型的主要区别在于压力应用。从注射时间到铸造过程中金属凝固,高压一直保持。另一方面,注塑成型涉及在高压下将熔融塑料或聚合物注入型腔,然后冷却以形成固体部件。
性能
它可制造出具有优异机械性能和表面光洁度的零件。
能够实现复杂的形状和特征,比如底切、内部通道、深槽和不规则轮廓。
工具和设备成本低。
它可以生产这些大尺寸的零件。
多种材料选择;铝、不锈钢、碳钢、锌、镁等等。
缺点
铸造部件可能需要后期加工才能满足尺寸和精加工规格。
与塑料成型相比,出现孔隙、空隙和其他缺陷的风险相对较大。
适合的应用
消费品、医疗设备、电子零件及外壳、工业齿轮和衬套、体育用品、家用电器和储存容器。
结语
我们已经讨论了什么是铸造以及其他相关方面、材料、类型、优点、缺点和应用。总体而言,它是一种用于制造复杂金属零件的突出技术,具有高强度、结构完整性、耐磨和耐腐蚀性以及精密公差,适用于众多工业应用。从砂型到模铸和失铸,铸造方法多种多样,可以满足无数制造需求。但是,选择适合您的零件的铸造技术或方法取决于材料类型、设计复杂性、精度、生产规模、预算等。
铸造技术有很多种,每种技术都有独特的特点和优势;砂型铸造、模压铸造和熔模铸造就是其中几种。但是,使用哪种方法取决于设计部件的原材料类型和规格。本文将讨论铸造工艺、技术、兼容的金属和合金、优点和缺点,以提供全面的概述。
什么是铸造?
它指的是熔融金属在凝固时形成几何形状而制成的任何金属和合金部件。液态金属会呈现出包含它的腔体的几何形状。浇注后,材料会流过腔体(模具)内的每个角落并捕捉每个细节。然后,将部件顶出到模具腔体中。
追溯其历史,铸造工艺可追溯到七千年前(约公元前3200年) 在古代 美索不达米亚和中国 将铜转化为各种有用的物品。公元前 645 年后,砂型铸造成为工具和炊具最突出的制造方法之一。
在现代制造时代,随着金属铸造工艺能力的不断发展,它已融入所有行业。它可以以低廉的价格制造精密而复杂的部件,尤其是在大批量生产中。模具、铸模或其他形式的型腔可以生产数千到数百万个相同的零件。然而,砂模和熔模只能使用一次,这对于原型项目来说是经济的。此外,铸造部件保留了原有的机械和物理性能。
铸造是如何进行的?
铸造工艺的基本工作机理
铸造或铸模工艺涉及两种不同的方法,使用腔体模型和可承受多次循环的精密模具。以下是与其工作相关的一些术语;
模型:这是用金属、塑料或木材制作的用于塑造模具的所需部件的全尺寸复制品。
型芯和型腔:型腔是指勾勒出铸件外部特征的空心部分,而型芯则形成内部特征,例如孔和通道。
浇注系统:引导和控制金属液从浇注炉流向型腔的通道。它包括浇口、流道和浇口等组件。
冒口:模具中的储存器,用于将熔融金属供给铸件以补偿凝固过程中的收缩,确保铸件无空洞和缺陷。
接下来我们来一步步阐述一下casting的工作原理。
步骤 1:创建模具型腔
图案是创建空腔所必需的,因为它充当所需形状的主体。复制品或图案可以用木头、塑料或蜡制成。随后,在图案设计和制造中需要考虑一些因素,例如尺寸调节以适应收缩余量、拔模角度以方便拆卸、空心部分的芯模等。
制作完模型后,将其放入一个造型盒中,四周环绕着沙子或陶瓷等造型材料。然后,它会捕捉形状并在弹出时离开型腔。然而,永久模具型腔是采用先进的制造技术制成的,例如 数控 和 电火花加工 不锈钢或铝。
步骤2:倒入熔融材料
首先,材料熔炼涉及电弧、感应或坩埚,具体取决于铸件尺寸。例如,大型铸件需要大型熔炉来熔化原材料,并在浇注前使用小型钢包进行转移。
浇注是通过手动操作坩埚或机械和液压倾倒来完成的。然而,连铸机可以在模具沿着生产线移动时自动将熔融材料倒入浇注底座。温度根据铸造材料的熔点而变化。例如,不锈钢铸件高达 1000℃-1250℃。接下来,浇口和浇注系统将液体材料引导到型腔。
第四步:冷却固化
一旦液态金属捕捉到所有腔体的细节,它就会在特定时间内冷却并凝固。冷却系统可能涉及通道和通道来控制冷却速度。同时,冷却时间取决于铸件的尺寸、复杂程度和材料类型。
在凝固过程中,被称为晶核的微小固体颗粒聚集在一起并开始晶体生长,最终形成相应材料的晶粒结构。这种机制允许恢复原有的性能。
步骤 4:取出铸造产品
最后,将产品从模具中取出。如果模具是可膨胀的(砂型或熔模铸造),操作员或机械系统会将其破坏以弹出最终部件。另一方面,对于可重复使用的模具和冲模,顶出机构会取出金属铸造产品。然后,清洁和后处理可确保尺寸精度和成品质量。
现在我们知道了什么是铸造以及它的基本工作机制,让我们来讨论一下铸造的类型有哪些。
不同类型的铸造方法
随着各行各业不断寻求更精确、更复杂的铸件,金属铸造技术也在同时开发新方法和新技术。您可以找到多种类型的铸造方法,例如砂型或硅型铸造和压铸方法,每种方法都具有一些独特的功能。这些技术的比较分析(流程、优势和应用)可以帮助您确定哪种技术最适合您的项目。
以下是制造业中常见的铸造方法。
砂模铸造
砂型铸造法使用紧密堆积的细小硅基材料或砂粒来制作模具。模具包括两个部分:上模和下模(上半部分和下半部分)。同时,将熔融金属倒入由这两个部分形成的型腔中。这种机制还可确保精确对准、易于操作、复杂形状和高效浇注。
产品优点
模具制造和铸造工艺简单,且工具成本非常低。
砂型铸造几乎与所有合金都兼容,包括黑色金属和有色金属。
形状和尺寸灵活。可铸造重量超过200吨的零件。
虽然尺寸精度较低,但后处理简单且耗时较少。
应用: 活塞、衬套、电子元件、阀门、轴承、发动机曲轴箱、工厂机械等。
精密铸造
- 熔模铸造工艺 比砂型铸造相对复杂。它涉及使用连接在中央蜡浇口中的蜡模来准备模具。然后,陶瓷等耐火材料围绕该网络。接下来,加热模具将耐火材料内的蜡模熔化,并使型腔具有光滑的表面,这也是它也称为失蜡铸造的原因。然后,将液体倒入该型腔中,并在凝固完成后破坏模具以取出零件。
产品优点
使用蜡模可以制作空心部分、底切和内部通道,而无需插入芯。
晶粒结构细化,表面光洁度更好。
尺寸精度高(±0.1mm)
具有复杂几何形状的薄壁零件
应用: 军用和飞机部件,如发动机零件、工业设备部件、汽车发动机和排气系统、医疗植入物和仪器等。
压铸
这种铸造使用由坚固的材料制成的永久模具(称为模具),例如硬化工具钢。它通常用于锌、铝、铜和锡等材料。 压铸工艺 包括在熔炉中熔化原材料,熔炉可能连接到铸造机,也可能不连接到铸造机。然后,液压柱塞或注射机构将液体输送到模具中。同时,压力可达到 25000 psi。
产品优点
整个生产周期内严格的公差和一致性
后期处理操作要求较低
大批量生产具有成本效益
应用: 它的应用范围很广,例如汽车零件、飞机涡轮叶片和机身、电器外壳、工业产品、机床和家用电器等。
离心铸造
离心铸造法或旋转铸造法使用绕轴旋转的圆柱形模具,将液态金属倒入旋转的模具中。离心力将浇注的金属推向模具壁,形成均匀的层。然后,凝固形成具有特定厚度的模具形状。
产品优点
由于金属液连续供给,因此不存在孔隙
由于离心铸造部件向内凝固,因此出现气穴和缩孔的风险极小。
由于没有冒口,因此减少了浇注阶段的材料消耗。
致密且均匀的谷物结构。
应用: 这种铸造制造主要用于制造对称物品,例如空心圆柱体,轴套,管道,压力容器,圆盘形状等。
低压铸造
附在铸造机上的浇注炉或加压炉的压力通常为 0.02 至 0.07 Mpa。浇注炉保持在铸件下方,用升液管将金属液压到上方,然后将其转移到型腔中。持续的压力是填充型腔所必需的。一旦型腔被填满,冷却通道就会以受控的方式冷却模具,直到完全凝固。
产品优点
低压可以精确控制填充并消除湍流,减少孔隙率和收缩等缺陷。
高精度和精细的铸造。
低压铸造工艺适用于铝合金等各种有色材料。
光滑的填充还可以铸造尖角和复杂的几何形状。
应用: 气缸轮毂和框架、轮毂、厨具、定制空心和复杂型材、配件、电子设备部件等。
重力压铸
重力压铸工艺中的金属浇注不需要压力注射或柱塞机制。它涉及利用重力将材料从熔炉或钢包转移到模具中。在填充完成之前,没有其他力影响流动。此外,它主要适用于熔点较低的有色合金,例如铜、锌、铝和镁。
产品优点
定义结构、更好的机械性能和表面光洁度。
由于没有压力流,最终部件的孔隙率最小。
由于不需要注射机制,它比其他永久模具具有更简单的工具。
应用: 重力压铸在许多行业中具有广泛的应用,包括汽车零部件、工业机械零件、航空发动机和外壳元件、装饰品、家用电器零件等。
真空压铸
顾名思义, 真空铸造工艺 将熔融状态的金属或塑料放入真空中成型。一般来说,在此过程中,泵或类似装置会抽走模具内的所有空气。
硅胶模具(如聚氨酯)用于橡胶和塑料成型。但是,其他类型的模具和压模也适用于真空铸造不同材料。此外,这种铸造制造模仿了注塑技术的一些特性。这种真空铸造策略也适用于标准压铸,以最大限度地降低空气滞留的风险。
产品优点
高精度和准确度,特别是对于 3D 打印模具的项目。
铸工精细,细节复杂
它消除了铸造金属内部形成孔隙的风险。
能够很好地铸造较薄壁的零件
应用: 功能塑料原型、医疗植入物和假肢、消费品、汽车车身面板和其他部件、食品加工部件等。
挤压压铸
该方法通过在模具内压制液态和半固态材料来制造零件。首先,液态金属填充加热的开放式模具,然后上部零件将其关闭并通过连接的液压板或其他合适的机制施加压力。零件在压力下凝固并提供更好的机械性能特征。此外,它也被称为液态金属锻造。
挤压压铸有两种类型:直接压铸和间接压铸。在直接压铸过程中,熔融金属填充模具,上半部分闭合模具。另一方面,间接压铸首先将熔融金属注入型腔,然后通过冲头或柱塞施加高压。
产品优点
优异的表面纹理和最小的孔隙率。
生产周期快。
挤压铸造可以生产出精确的(接近最终形状的)零件。
压制过程中的快速传热可产生精细的微观结构。
应用: 高强度汽车零部件(如底盘和发动机支架)、航空航天零件、工业齿轮和液压部件、医疗设备零件等。
消失模铸造
“消失模”之所以被称为“消失模”,是因为所需部件的聚苯乙烯泡沫模型负责产生最终形状。模型被放置在耐火材料内,在倒入液体材料后,耐火材料会熔化,并在凝固后形成形状。然后,打破模具就会露出部件。
产品优点
具有优异的表面质量和最少的后加工要求的复杂几何形状。
消失模铸造可与多种材料兼容,包括铁、不锈钢、铝和铜。
它简化了制造过程,减少了时间、劳动力和材料浪费。
应用: 用于测试的快速原型、汽车气缸盖和焊接件、管件、阀门、泵外壳等。
连续铸造
连续铸造包括在生产线上连续浇注、凝固和部件移除。设置和过程涉及钢包或熔炉,材料通过控制系统流入模腔。随后,模具中的冷却机制(水道)迅速降低温度。因此,在使模具部件明显冷却的同时,进一步喷水使它们恢复到室温。
产品优点
这是一个简单的过程,因为连续铸造不需要流道、浇口和冒口。
100% 额定产量,无材料浪费。
连铸自动化提高了效率和生产率。
应用:具有一致轮廓的零件,如梁、柱、棒、带、管等。
铸造所用材料
多种铁和有色合金适用于金属铸造工艺。下表简要说明了铸造材料、其特性和等级。
金属/合金 铸造等级 抗拉强度 抗疲劳 硬度 耐磨性 耐腐蚀性
镁 AZ91D、AM60、AM50 中 好 中 中 中
铝板 A356、6061、7075 中 优异 中 好 优异
铁 灰铸铁 (G3000)、球墨铸铁 (65-45-12) 高 高 高 高 低至中等
锌 锌合金 3、锌合金 5、ZA-8 中 低 中 中 好
铁板 碳钢 (AISI 1020)、不锈钢 (304、316) 优异 优异 优异 优异 中等至优秀
铜合金 黄铜(C36000)、青铜(C95400) 高 好 中 高 优异
铅合金 铅锡合金、铅锑合金 低 低 低 低 高
铸造的优点
复杂的形状和几何形状
铸造工艺可以创建复杂的形状和特征。例如,内部通道和腔体、底切、薄壁、空心部分、多部件组件、不对称几何形状等。同时,这种能力背后的原因是熔融金属可以在任何小腔体和尖角内流动。
材料的多功能性
它可以与多种金属和合金一起使用, 黑色金属和有色金属。例如,铁、钢、锌、铜、铝和铅合金。因此,广泛的材料多功能性使人们能够灵活地选择满足所需特性的最佳材料。此外,铸造难以加工或锻造的金属也很容易实现。
成本效益
对于小批量或原型,砂型铸造和其他膨胀型铸造具有成本效益。另一方面,永久压模铸造方法适用于大规模制造,因为一次性模具成本可以覆盖数百万个周期。总体而言,铸造是一种经济高效的制造方法。
尺寸范围
任何尺寸的部件都可以铸造,从几百克到 200 多吨。例如,小型摩托车发动机缸体到大型蒸汽涡轮机外壳和工业设备底座。
高强度和耐用性
通过控制冷却过程使模具凝固,确保晶粒结构均匀,并在所有方向上保持相同的机械性能(强度和韧性)。此外,热处理和合金化等先进技术可提高耐磨性、耐腐蚀性和整体耐用性。
减少浪费
浇口、进料口和流道产生的废料可通过重新熔化在后续循环或批次中重新使用。因此,铸造制造中的材料浪费最少,从而降低了生产成本并有利于环境可持续性。
铸造的缺点
初始成本和时间
模具安装成本和时间比其他制造方法的加工成本更高,尤其是永久性模具。它会影响小规模生产的单件生产成本。较长的安装和生产周期也会影响从设计到上市的时间。
表面光洁度和精度
在砂型、耐火材料铸造的工艺中,由于造型材料的特性,铸件表面常常粗糙,尺寸不一致,因此铸件产品需要进行修整、打磨等后加工。
缺陷和质量控制
在金属铸件中,可能会因滞留气体、流动湍流、冷却不均匀、质量控制过程复杂以及其他原因(例如孔隙、收缩、翘曲和夹杂物)而出现缺陷。这些缺陷会削弱物理结构和性能。
复杂过程控制
铸造的另一个缺点是工艺控制的复杂性,控制温度、流速、压力、冷却速度和固化时间等许多参数使得准确控制工艺变得具有挑战性。此外,熔融材料的冶金性能考虑也增加了复杂性。因此,缺陷品的百分比和后处理要求可能会增加。
铸造的工业应用
压铸件
接下来,让我们从多个领域的应用角度来谈谈铸造是什么。
汽车行业
从“压铸方法最初是为了制造复杂的汽车锌部件而发明的”这一事实可以看出,汽车行业铸造应用的多样性。在当前情况下,汽车严重依赖铸造技术来生产轻质耐用的部件,这些部件有助于提高燃油效率和性能,例如发动机缸体、气缸盖和传动部件。铸造能力可以使用插入芯和定制工具方法精确地制造这些部件的复杂性和复杂特征。同时,铝压铸有利于生产轻质耐用的部件。
由铝铸造而成的高强度、轻量化发动机部件。
底盘部件动力传动部件。
空调零件。
燃油进气系统、转向系统、变速箱等。
航空航天工业
铸造方法可以将镍基超级合金、铝合金和镁合金等轻质材料加工成复杂的航空航天部件。同时,受控的冷却和凝固增强了它们的性能。因此,它通过生产轻质耐用的部件使航空航天业受益,从而提高了飞机和航天器的燃油效率和性能。
因此,熔模铸造在航空航天工业中最为常见。然而,模具、消失模、砂型和其他铸造方法也很普遍。铸造工艺允许制造具有复杂几何形状和内部冷却通道的航空航天部件,例如发动机缸体、气缸盖和传动部件。其他应用包括:
发动机部件、涡轮叶片、燃油系统零件、起落架零件等。
泵壳入口和出口蜗壳。
液压系统元件。
控制室内部及部件。
消费品
铸造工艺能够制作复杂的设计,例如华丽的装饰、精致的厨房用具和耐用的炊具,因此适合制作许多消费品。这些物品采用熔模铸造、模铸、消失模铸造和砂型铸造等技术制造。由于精细的细节和美观性在这些应用中至关重要,因此铸造方法还可以确保腔壁表面光滑。
装饰品、墙钩、相框、灯具等。
门把手、门把手和其他类似的硬件。
厨房用具,例如锅铲、开瓶器、水槽水龙头、搅拌机底座和炉灶燃烧器。
工业设备和机械
铸造制造保持了原材料的原始特性,甚至可以通过添加填料和添加剂来提高其性能。因此,砂型、模具和其他铸造模具可以塑造高强度和耐腐蚀的合金,如不锈钢、碳合金和铝。此外,铸造还适用于大尺寸和重量的设计。因此,铸造可以为重型机械和工业设备生产坚固、耐用、耐磨和耐腐蚀的零件。例如,泵、变速箱、阀门、液压缸组件、破碎机颚式破碎机、传送带滚轮、定制外壳等。
医疗器械
生物相容性材料铬、钛、锆和钛合金也可以使用不同的技术进行精确铸造。精密铸造零件具有出色的光洁度、精度和复杂特性,这些特性对于医疗植入物和手术器械来说是必不可少的,以确保患者的安全。同时,砂型、模具和其他类型的模具也用于制造设备外壳、诊断设备部件和医疗家具。
其他一些具体的应用示例是;
定制髋关节置换、膝关节、脊柱和牙科植入物
心脏瓣膜框架、镊子和手术刀
手术剪和手术托盘
MRI 机器外壳和 CT 扫描仪框架
能源行业
不锈钢、镁、铝和锌合金等高强度材料的铸造可以为能源行业制造出能够承受高压力和恶劣化学和环境条件的部件和产品。此外,熔模铸造和压铸等工艺可确保精度和一致性,并将缺陷降至最低,这对于能源工厂的可靠性至关重要。
风力涡轮机部件,如轮毂、变速箱壳体和主机架,采用砂型和熔模铸造,具有高精度和结构完整性。
涡轮叶片、轮叶和燃烧室具有复杂的细节和严格的公差。
核反应堆压力容器、堆芯围带和蒸汽发生器零件。
太阳能电池板和电动汽车组件。
铸造与注塑成型的比较
铸造与注塑成型对比
从根本上讲 注塑工艺 同样是依靠熔料在预定形状的型腔内凝固的原理,但具体机制、能力、材料兼容性等各方面都有所不同,接下来分别阐述什么是铸造、什么是注塑成型,从中可以看出深度上的差异。
注塑工艺
这是一种主要用于批量生产热塑性塑料部件(少数热固性塑料和金属除外)的制造技术。液态塑料或金属在高压下注入模腔;材料在模具内流动,并在凝固后带走模腔的细节。此外,顶针或其他系统将部件从模具中取出。通常,注塑模具由高强度钢合金制成。
性能
各批次尺寸和整体质量一致
大批量时具有成本效益
生产周期快
高度自动化是可能的
它可以容纳二次插入物和其他类型的材料以形成单一物品。
缺点
对于小批量生产来说,高昂的工具和设备成本在经济上是昂贵的。
质量和结构完整性比铸造产品低。
材料的多功能性仅限于聚合物和少数金属。
大尺寸部件不适合注塑成型。
适合的应用
高强度汽车零部件、精密航空航天硬件、工业厂房机械、可靠能源组件、重型设备、医疗植入物等。
铸造过程
铸造,尤其是压铸模具与注塑成型相对相似;您可以将压铸模具与注塑模具联系起来。然而,压铸与注塑成型的主要区别在于压力应用。从注射时间到铸造过程中金属凝固,高压一直保持。另一方面,注塑成型涉及在高压下将熔融塑料或聚合物注入型腔,然后冷却以形成固体部件。
性能
它可制造出具有优异机械性能和表面光洁度的零件。
能够实现复杂的形状和特征,比如底切、内部通道、深槽和不规则轮廓。
工具和设备成本低。
它可以生产这些大尺寸的零件。
多种材料选择;铝、不锈钢、碳钢、锌、镁等等。
缺点
铸造部件可能需要后期加工才能满足尺寸和精加工规格。
与塑料成型相比,出现孔隙、空隙和其他缺陷的风险相对较大。
适合的应用
消费品、医疗设备、电子零件及外壳、工业齿轮和衬套、体育用品、家用电器和储存容器。
结语
我们已经讨论了什么是铸造以及其他相关方面、材料、类型、优点、缺点和应用。总体而言,它是一种用于制造复杂金属零件的突出技术,具有高强度、结构完整性、耐磨和耐腐蚀性以及精密公差,适用于众多工业应用。从砂型到模铸和失铸,铸造方法多种多样,可以满足无数制造需求。但是,选择适合您的零件的铸造技术或方法取决于材料类型、设计复杂性、精度、生产规模、预算等。
招商项目
更多项目
【招商】文创之都引领经济增长新动能
2025-07-18
【北京招商】北京市政务服务智能化升级助力经济发展 150项自助办理服务落地实施
2025-07-18
【北京招商】个体工商户登记改革加速 北京市场活力显著提升
2025-07-18
【招商】首都工商深化"开墙打洞"长效治理新机制
2025-07-18
【北京招商】新能源科技园落户京南 打造绿色创新高地
2025-07-18
【大兴区招商】大兴区拆除低端业态建湿地公园 打造京南生态绿肺
2025-07-18
【招商】魏善庄镇创新政务服务模式助力乡村振兴
2025-07-18
【北京招商】北京经开区打造国际人才社区 构筑引才留才新高地
2025-07-18
【招商】北京开发区安全托管显成效 25家汽修企业筑牢安全管理体系
2025-07-18
【密云区招商】德国博马科技落址密云建中国研发中心
2025-07-18
潮流盛会激活青年消费 资源整合力促招商引资
2025-07-18
【密云区招商】北京农林科学院调研密云区森林健康经营项目成效
2025-07-18
优惠政策
更多政策
上海市崇明区长兴镇人民政府关于新凤翔公司西侧围墙修缮工程项目的批复
2025-03-14
崇明关于印发《东平镇镇属企业、民非组织负责人考核实施意见(试行)》的通知
2025-02-25
承德市人民政府关于河北美富淦冶金材料科技有限公司“12·03”叉车碰撞事故调查报告的批复
2025-02-11
梅州市人民政府办公室关于公布梅州城区(不含梅县区)2023年国有建设用地基准地价的通知
2025-02-05
福建省人民政府关于龙岩市永定区光坑水库工程建设农用地转用和土地征收的批复
2025-01-26
济宁市兖州区人民政府关于分解落实2025年政府工作报告任务目标的通知
2025-01-26
唐山市人民政府关于唐山市开平片区和国际旅游岛部分单元、街区、地块详细规划的批复
2025-01-26
中山市人民政府关于中山市港口镇石特工业片区(0801单元)控制性详细规划一般修改的批复
2025-01-24
产业园区
招商引资
招商政策
投资流程
土地招拍挂
厂房价格
注册公司
优惠政策
投资流程
外商投资
买地自建
厂房租赁
写字楼租赁
公司注册
优惠政策

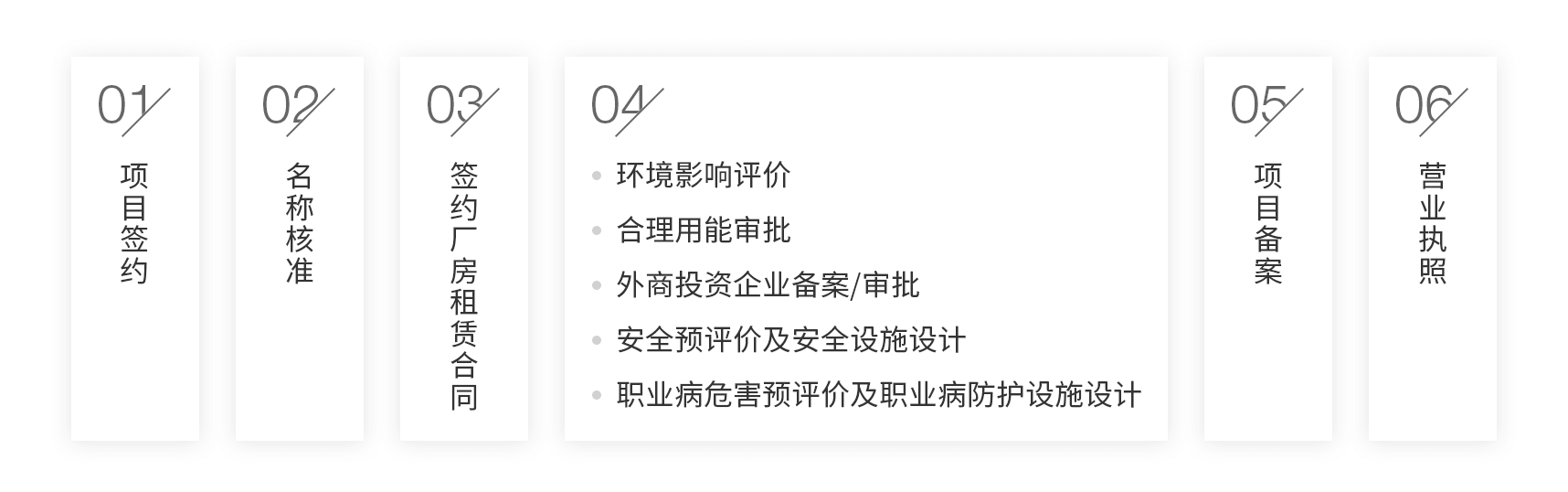
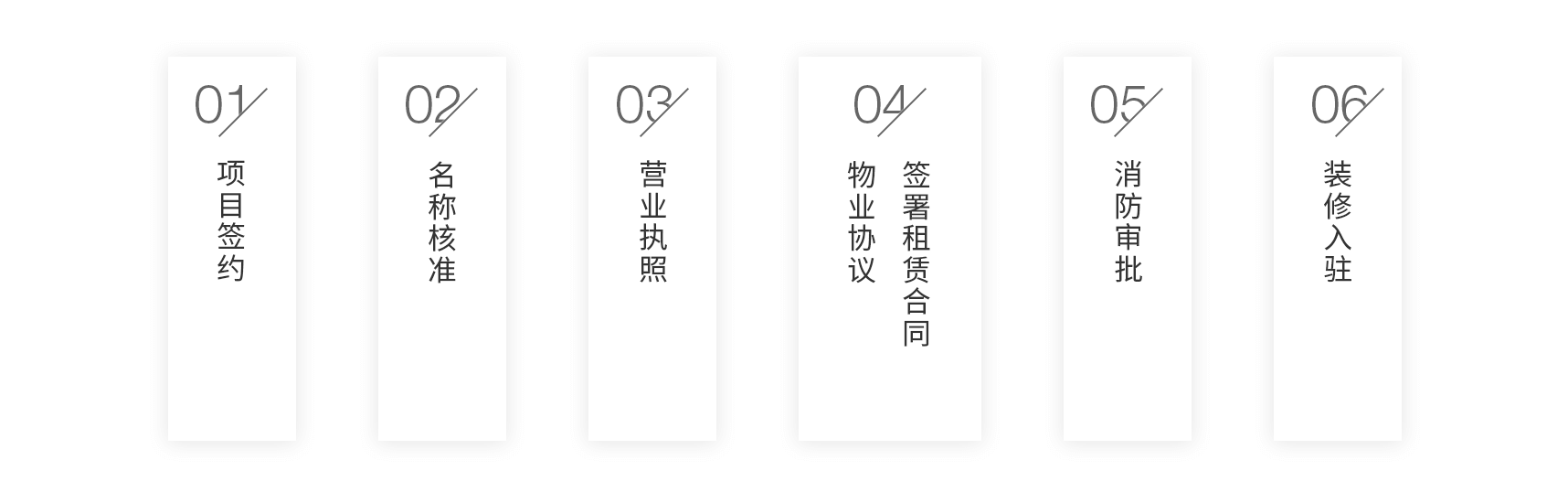
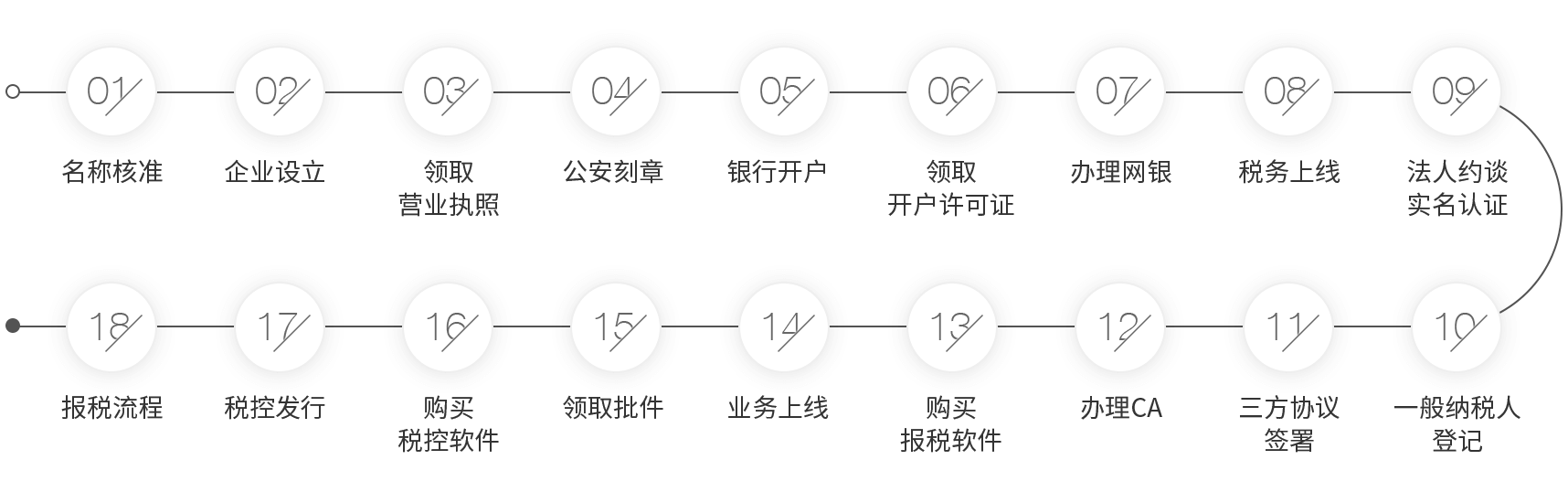
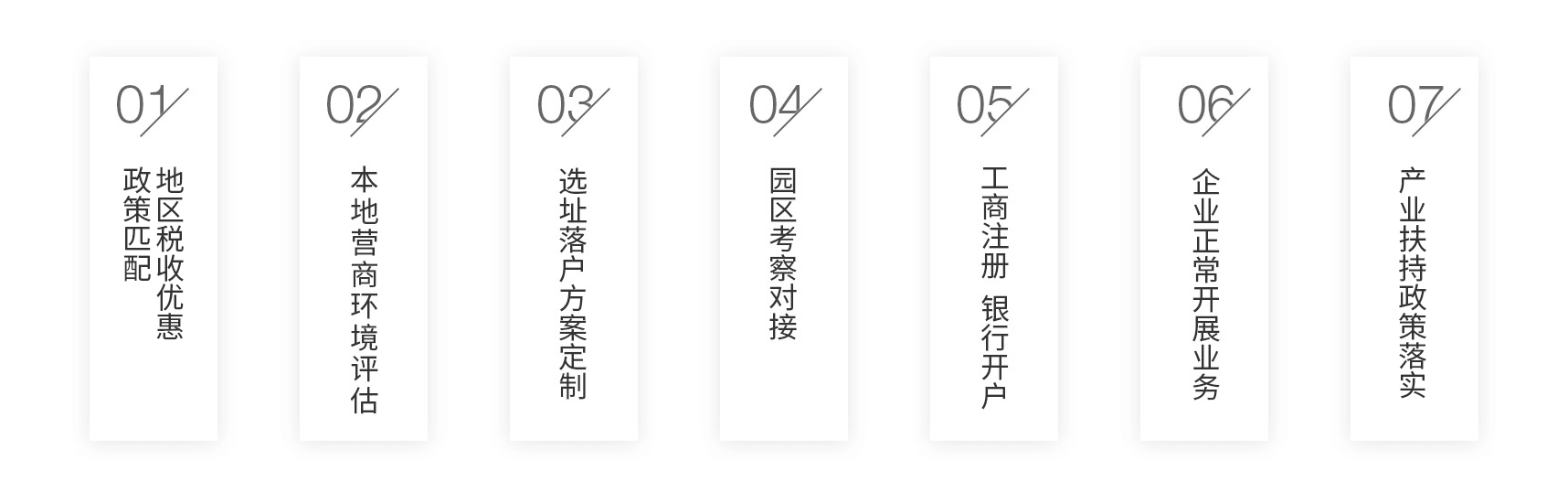
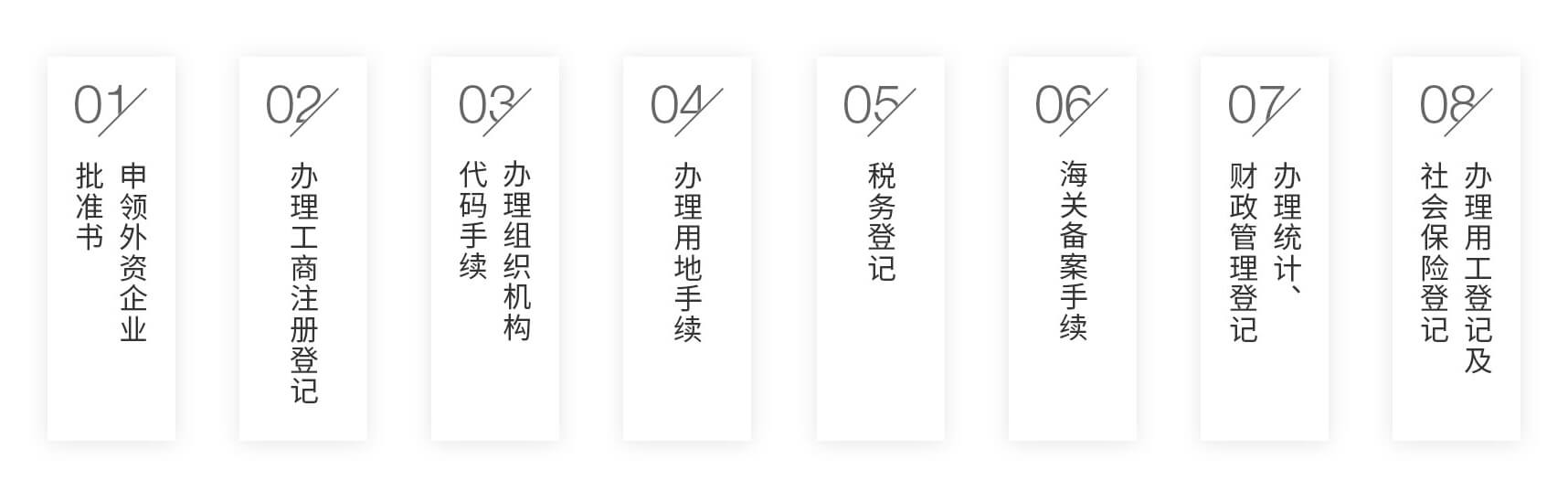

- 联系我们
- 企业入驻

立即获取